Article: Optimise maintenance efficiency with real-time asset tracking
To ensure efficient processes in a complex company like Deutsche Bahn, you need to maintain an overview of all key assets in day-to-day operations. TracE, which stands for "Tracking Everywhere", provides detailed asset tracking: real-time localisation for materials or any other kind of object.
Especially when carrying out maintenance, you need to be able to precisely locate the "assets" required for your day-to-day work at any time: whether load carriers, spare parts or expensive tools. Don't search – locate!
"By pooling market expertise and integrating it into Deutsche Bahn, we can provide a holistic range of services for different business units within the DB Group. This facilitates process transparency, process optimisation and partial automation in maintenance depots, which has a positive impact on process lead times."
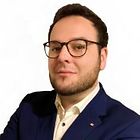
Determine and locate current stock at any time
With seamless tracking of assets and integration into asset management systems, we achieve maximum efficiency that goes beyond merely locating assets: assets can also be automatically logged in and out so that the inventory is always up to date. This means that parts and maintenance items can be viewed digitally at any time and in real time. And as we use different indoor and outdoor location technologies depending on the environment, we can select the best possible technology for each use case.
How we support maintenance
Everything in view with asset tracking
Transparency for materials management and logistics: each object defined as an "asset" is tagged with tracking tags so that it can be individually located and tracked at any time.
Process optimisation and shorter lead times
Individually configured dashboards can be used to display assets or analyse steps in a process, which also means that lead times can be measured in individual process steps and thresholds can be defined.
Process automation
Predefined events allow processes such as a collection order to be triggered independently or repeat orders to be started. In practice, this could mean that the forklift management system creates a collection order automatically whenever an asset is placed in a particular area. This asset is then collected by a forklift truck without any manual intervention.
Do you want to be able to pinpoint the precise location of movable and fixed objects?
We look forward to talking to you about asset tracking and the digitalisation of maintenance.